
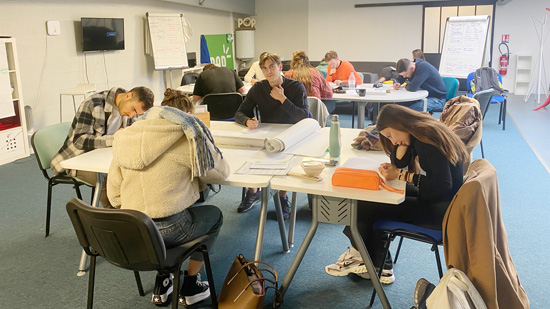
The innovative aspect of this course lies in its immersive approach. For 2 days, the group traveled to Nantes and set up in a "company school". "On site, everything was standardized to make employee tasks clearer, in order to avoid wasting time, materials, and so on" explained Servane.
Lean management is an organizational method modeled on the Toyota production system. The sources of waste in the company are identified (transport, inventory management, defects, etc.) and optimization steps are taken. Staff are involved and encouraged to report any problems they encounter. This method also helps to reduce tensions, bring up and deal with problems on the ground, and share common goals.
Servane:
We were able to see in practice what could be put in place, and carried out a number of role-playing exercises. I'm going back to the company in a few weeks as part of my vocational training contract. Lean management is already well established there. The fact that I've taken this course means I'm comfortable with the vocabulary and able to apply certain techniques.
Various methods were presented to the students: the 8-wastes method, as well as weekly POP team meetings, the 5S method and visual performance management using Obeya, for example.
For Hugo:
Lean management is also a way of thinking, of optimizing things over time without changing the value of the product. It was mainly developed for the industrial sector, but could also be used to set up a design office, for example.
At the end of the course, students obtained a certification: the Yellow Belt. Recognized in the Lean field and by companies, it offers students a real advantage on their résumés.