
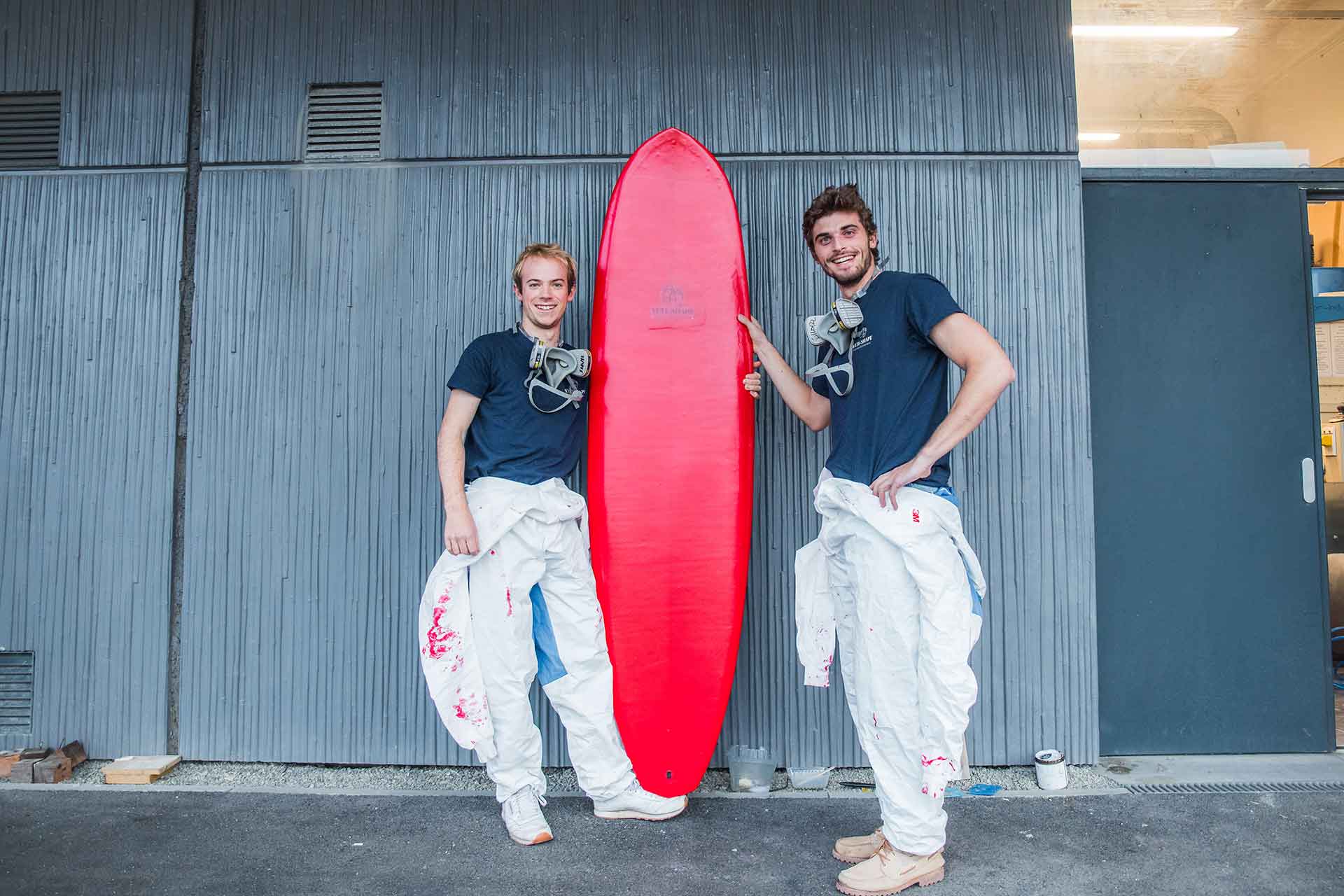
What is Yetishape's ambition?
Our first aim is to make surfboards to sell them to the Bureau de la glisse* in order to get the associations working together. Eventually, we would like to allow ENSTA Bretagne students to benefit from it and offer access to the surfboards on a free basis. We have now designed our first two surfboards. We were able to surf with the first surfboard in Carnac during our internship and we were pretty satisfied with the result! We are currently building two new surfboards.
* The Bureau de la glisse (BDG) is a students' union club.
How did you learn to make surfboards?
We taught ourselves by watching YouTube tutorials. As we are now more experienced, we've started to pass on our knowledge to other students, which is very satisfying. After receiving chemical hazard training on the school premises, we were allowed to use the campus facilities. This was required by health and safety standards as we sometimes have to handle toxic products.
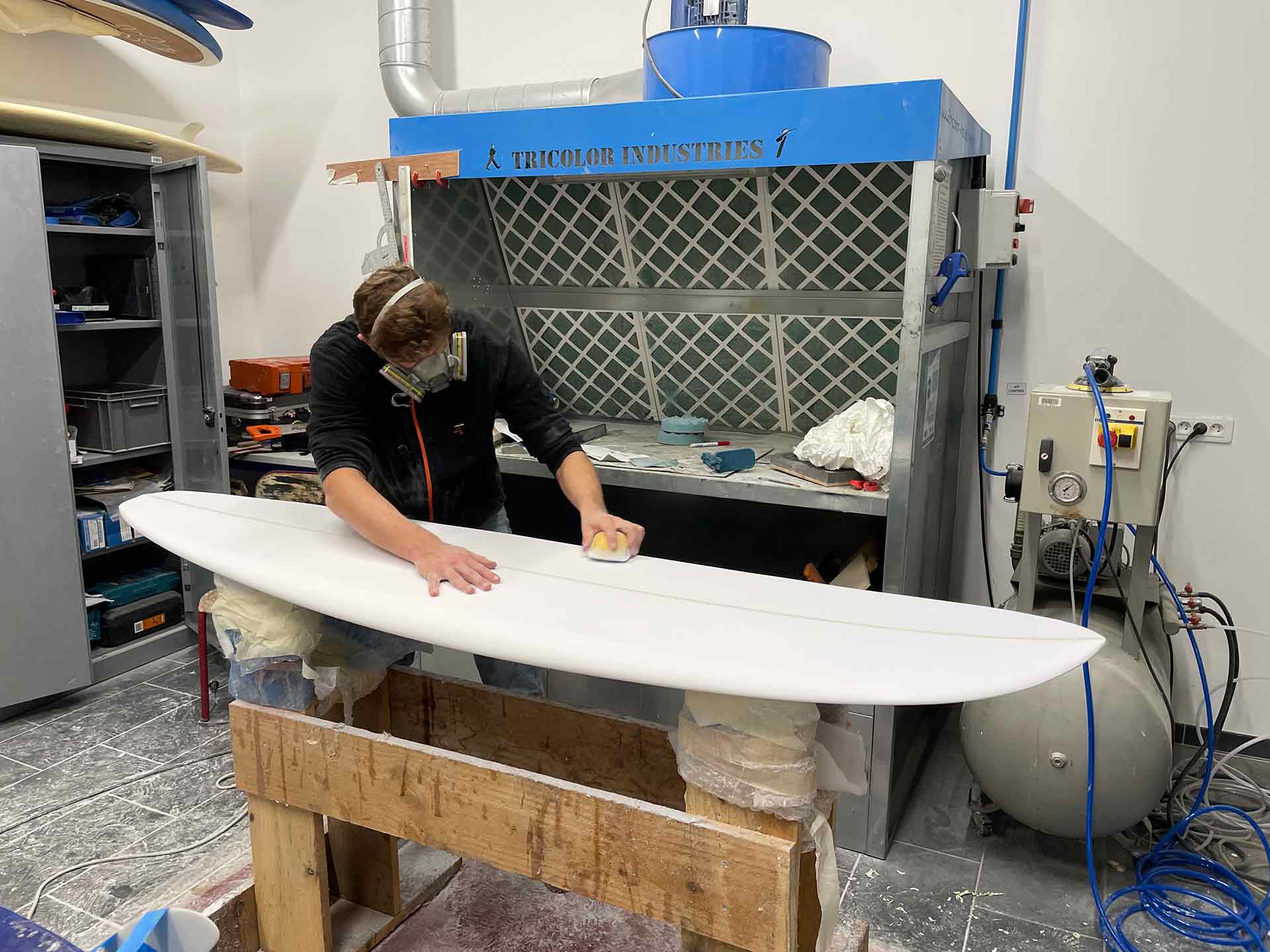
What are the main steps involved in making a surfboard?
- First step: Shaping
From a thinned-out block of polyurethane foam, the outline of the surfboard is made in order to create the "rocker".
- Second step: Stratification
A base and catalyst are poured onto the fiberglass and the resin is then spread and joined up with the sides. After leaving to dry for a few days, the operation is repeated on the other side and the fin plugs are added to allow the fins and leash plug to be fastened to the surfboard.
- Third step: Finishings
The hot-coat resin without pigment is first added and then sanded in order to apply the finish coat. The final step is then to polish the surfboard.
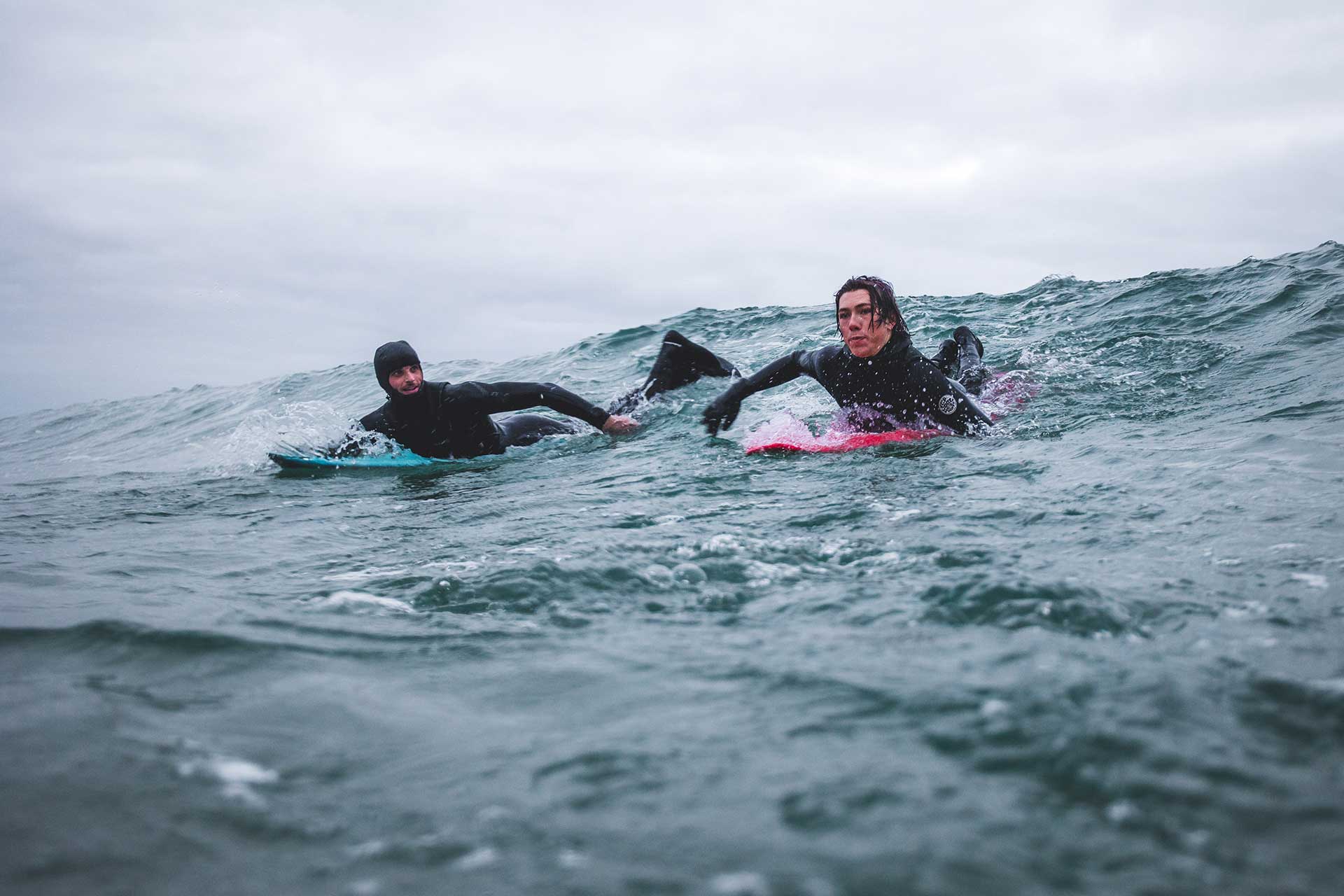
What unexpected things did you come up against when designing your first surfboard?
We learned the hard way that resin dries very, very quickly. When resin ran into my hair, I had to cut off a strand of it.
When applying the last coat of resin, the rack broke and the surfboard fell onto the floor, like toast, buttered side down. The small residues on the ground stuck to the surfboard, leaving it with a slightly flaky appearance.
How does the surfboard testing phase go?
In the team, we are lucky to have as test supervisors both Mathieu and Mattéo (junior surfing semi-finalist and vice-champion of Brittany in the longboard prospect category) to test our surfboards and give us their feedback so that we can improve design.
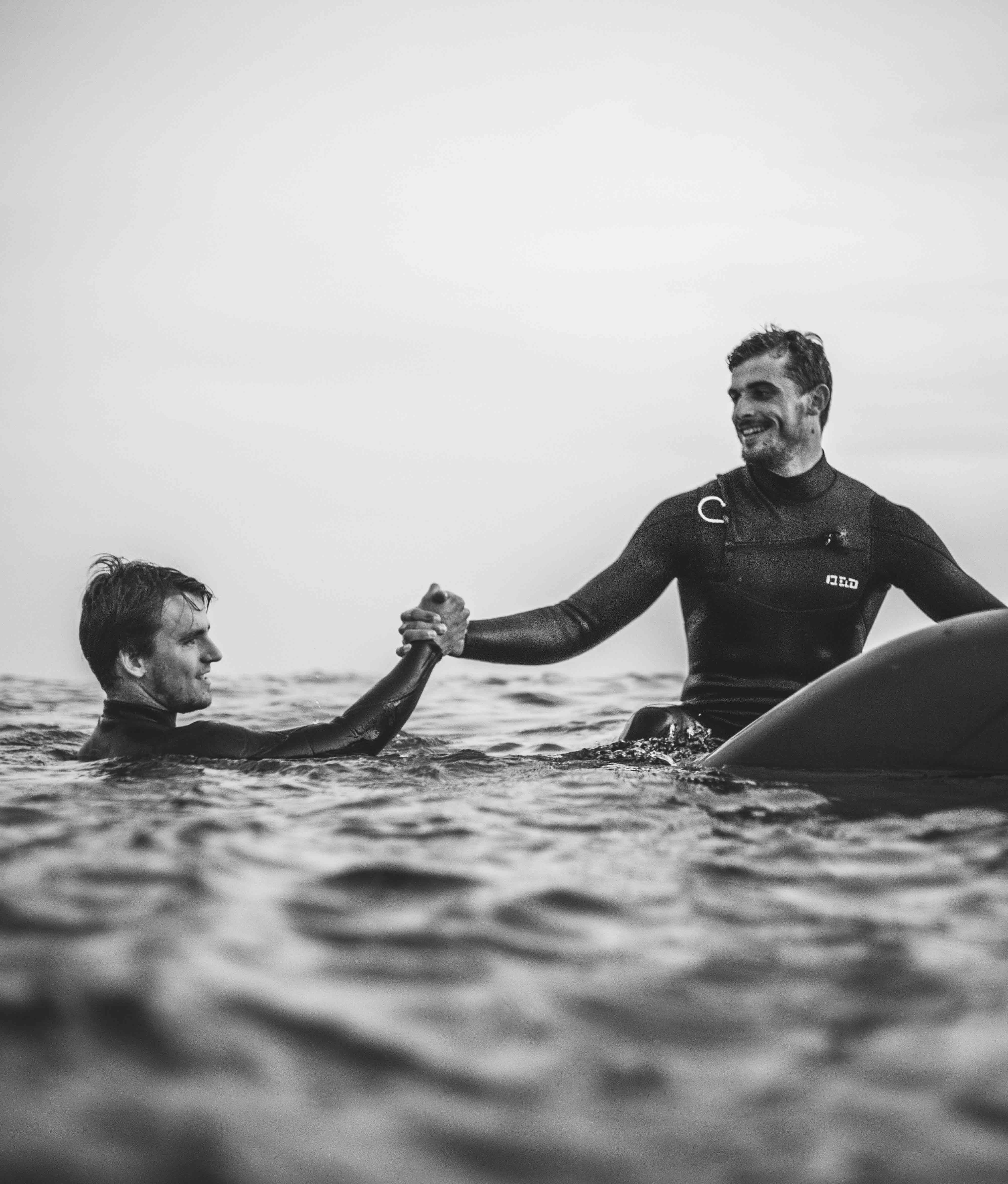
What is the ambiance like in your association?
We're first and foremost a group of friends. We always have lots of ideas in mind and the desire to do more; it feels a bit like a startup. We also have good times together, especially when we go surfing, when we meet up at the workshop to work on a new surfboard or when we receive new t shirts with the logo of the association.
What are your future projects?
We're working on a third and fourth surfboard. Eventually, our goal would be to open up the sale of our surfboards to the general public. We would like to take such an opportunity to change a few things when designing the surfboards. We recently switched to using epoxy resin to increase safety in the manufacturing of the surfboards. In parallel, we'd like to start shooting a surfing film to show at a festival.