
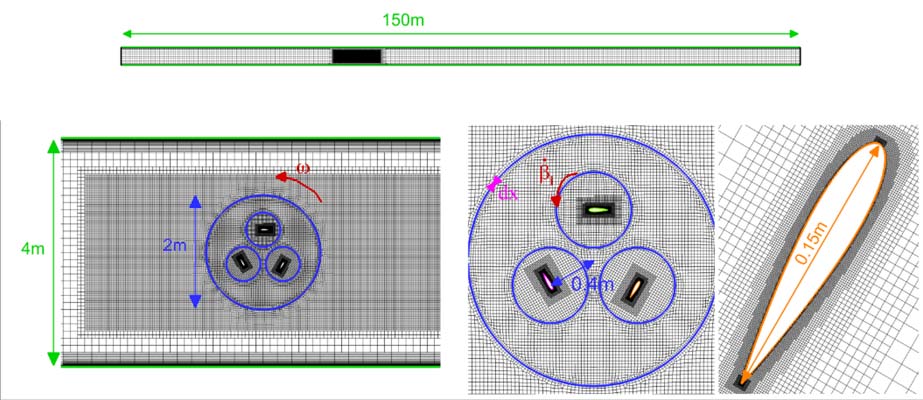
Ensuring precise 360° thrust on a ship is no easy task. The Voith Schneider Propeller has been used to solve this problem since the 1950s. Its design features the rotation of multiple blades around a main axis, combined with the movement of each blade around its own secondary axis.
However, changing the pitch of the blades is based on a mechanical system that does not allow for the transition from “high” to “low” speed operation and vice versa.
An all-electric solution
To remedy this problem, teams from the French Naval Academy (École Navale) and ENSTA are working on an innovative solution: an all-electric vertical axis thruster. This system uses a main motor to rotate the blades and a motor for each blade to give it the optimal orientation for the desired propulsion. The actuators for each blade are electric, thus replacing the mechanical systems.
The advantage?
This ‘all-electric’ solution overcomes the limitations of mechanical drives,” explains Frédéric Hauville, Associate professor at the French Naval Academy (École Navale) and a specialist in fluid-structure interactions. “We can now generate any motion for each blade, allowing us to study a wide range of kinematics.
The orientation of the blades in relation to the direction of the ship is known as the “pitch law”.
The challenge of our project is to determine the optimal pitch laws to maximize propulsive power, and then to optimize the control and performance of the thruster using machine learning methods,
explains Matthieu Sacher, Associate professor at ENSTA and a specialist in fluid-structure.
A first thesis carried out by Guillaume Fasse at the French Naval Academy (École Navale), in partnership with ENSTA and French National Institute for Ocean Science and Technology (IFREMER), led to an initial optimization of the thruster’s hydrodynamic performance. Since 2023, the three organizations have been pursuing the development of the thruster as part of the SHIVA project, funded by the French Defense Innovation Agency (AID) and awarded the IngéBlue label.
Full scale tests scheduled for early 2026
A demonstrator equipped with 6 blades (a 4.2 kW main motor and 200 W for each secondary motor) is currently under construction. At ENSTA’s IRDL[1] Mechanics Laboratory, a CNRS Joint Research Unit, Guillaume Fasse is implementing thruster optimization methods, while at the French Naval Academy Research Institute (IRENav), Clément Douche is designing the future 6-blade prototype and Florent Becker is in charge of motor control.
The prototype is expected to be completed in February 2025, with ship model basin testing of the thruster’s behavior in relation to the hull scheduled for fall 2025.
In 2026, the propulsive performance of the thruster will be tested on a military vessel in the DGA Hydrodynamic Techniques Center’s ship model basin and on a WASP demonstrator in real-life conditions.